Control of Hydrogen Porosity by optimizing analysis RPT samples
The Reduced Pressure Tester (RPT) can be a very effective tool to control hydrogen porosity in aluminum castings, when used as part of a structured process. Unfortunately, many foundries do not use the reduced pressure test to its full capability. To evaluate RPT samples, most foundries cut the part on a band saw, belt sand the cut surface, then compare to a chart.
Replacing the “cut and grind” process with a porosity analysis system to measure specific gravity is a safer, quicker, and more accurate method to analyze RPT samples.
CASE STUDY 1
A major manufacturer of cast precision parts for the automotive industry was experiencing a high level of customer returns for hydrogen porosity on the machined surface of the part. In some cases the return rates would be over 20%.
To analyze and control the porosity issue at the foundry, a Reduced Pressure Tester and Porosity Analysis System was implemented on the shop floor.
Step 1 – Develop Target S.G. The first step in developing foundry process control procedures for hydrogen porosity is to correlate the specific gravity of RPT samples to good and bad castings. Using this method it was determined that a specific gravity of 2.58 or higher yielded an acceptable casting while RPT samples with specific gravity readings under 2.58 meant the melt may not yield a good part. Knowing this information, the target for a newly degassed melt was set at 2.62 with a minimum of 2.58 required to cast.
Step 2 – Determine Degas Time With the specific gravity target defined, step 2 is to determine the standard degassing time for the melt. In this case it was determined that 20 minutes of degassing for each holding furnace (16 furnaces in total) would yield a RPT specific gravity at 2.62 or higher.
Step 3 – Implement Procedure The start of shift degas time was implemented. Metal from the degassed furnaces would be used throughout the shift then the furnace replenished and degassed again to start the next shift.
Step 4 – Monitor and Adjust To understand the melt quality throughout the entire shift, RPT samples were produced and specific gravity measured at the start of shift, end of shift, and various times in-between. As chart #1 shows, the melt would meet the specific gravity target to begin the shift but degrade throughout the shift. From this data it was easily determined that an additional degassing event must occur around mid-shift. Mid-shift degassing was implemented as a standard operating procedure and part of the Company’s quality control system.
RESULTS
As shown in Chart #2, the melt quality is under much better control after proper implementation of the RPT and Porosity Analysis system and as expected from these results, customer returns for porosity have been dramatically reduced.
CASE STUDY 2
Whereas the average part size produced by the automotive supplier in Case Study 1 was about 1/3lb, Specialized Castings of Greenville, Ohio produces parts in the range of 500 to 1200 lbs. These parts are typically one off parts for the blow molding industry. For Specialized Castings, porosity is not a structural concern but rather a cosmetic issue for their customers.
Using a Palmer RPT machine and Porosity Analysis System, the same process steps as in Case 1 were followed: 1) Determine Specific Gravity target 2) Determine degas time 3) Implement procedure 4) monitor and adjust.
Results
Using the Porosity Analysis System and the newly developed specific gravity target, Specialized Castings was able to update their Standard Operating Procedures to ensure the target specific gravity was met prior to pouring. “It was like we were operating blind” stated Jeff Deitering, President of Specialized Castings. “We now have a defined target that gives us confidence the melt is good.”
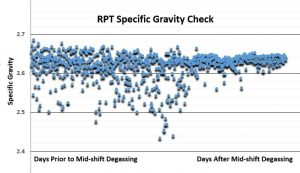
Article Takeaways:
- Increase accuracy of RPT sample evaluation by using Specific Gravity
- Develop RPT target number to improve casting quality and reduce scrap
- Use target numbers to determine degassing time and efficiency
- Greatly reduce cycle time while improving the safety factor
For a PDF version of this case study click here.
Contact: Brad Hohenstein
Authored: Brad Hohenstein (December 15, 2017)
Related Links: