Palmer Rotary Inert Degasser (RID)
A durable low cost solution to degassing 40 to 3,000 lb crucibles.
Reducing the hydrogen (gas content) of the aluminum melt prior to casting is one of the most important components of casting quality control in the foundry. The process of removing the hydrogen is called degassing. One of the most effective degassing methods is Rotary Inert degassing with an inert dry gas such as nitrogen, argon, or special blend. Degassing of aluminum is based on the principle that dissolved hydrogen gas will move from an area of high concentration (in the melt) to an area of low concentration (in the inert gas). Hydrogen gas disperses in molten metal as it would if it were released in any confined space. It will maintain a constant concentration throughout the melt. Hydrogen gas can migrate in the molten aluminum almost as fast as it can in air. Therefore, it is unnecessary to bring every ounce of metal in contact with the inert gas. The efficiency of aluminum degassing is determined by two factors, the transfer rate across the metal/gas interface and the total surface area available for transfer.
Rotary degassing works on the principle of increasing the surface area of an insert gas exposed to the metal. The larger surface area increases the rate of transfer from metal to the inert gas. The smaller the bubble size for a given volume of gas, the greater is the surface area. For example, a 1” diameter bubble of gas has a surface area of 6 square inches. If the same bubble is divided into 1/16” diameter bubbles, the surface area is increased to 96 square inches. In other words, if the same volume of gas is used and the diameter of the bubbles are reduced to 1/16th the original diameter, the total surface area is increased by a factor of 16. The smaller bubbles disturb the surface of the melt less reducing additional hydrogen pickup from humid atmospheres.
Most RID units on the market are designed to divide or chop the larger inert gas bubbles into smaller bubbles in order to effectively remove the hydrogen from the melt. However, many of these systems use expensive complicated rotor and shaft designs which add to the cost and longevity of the shaft and rotor. The beauty of the Palmer degassing unit is the innovative design of the “rotating lance” which eliminates the need for a shaft and rotor assembly. Slots are designed into the end of the rotating lance that very effectively cut the inert gas bubbles into a finely dispersed inert gas bubble throughout the melt. In addition to being less costly than the typical shaft and rotor design, the rotating lance is more durable requiring less down time.
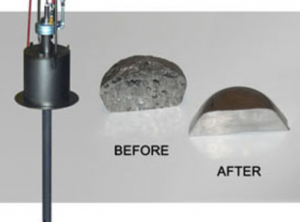
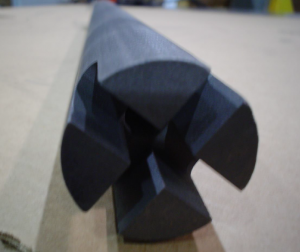
Rotary Inert Degasser – Features
- Low Cost With High Efficiency
- Stainless Steel Construction
- Variable Speed Air Motor
- Portable and Lightweight – Under 50 lbs
- Versatile – Can be used in dip-out or crucible furnaces with capacities from 40 lbs to 3000 lbs
- Unique one piece rotating lance design provides effective degassing while reducing costs by eliminating shaft / impellor design
- Eliminates use of hazardous degassing tablets and chlorine or Freon gasses.
General Specifications
- Motor Horsepower – 3/4 HP
- Motor RPM – 3600 RPM Variable Speed
- Lances – 24″ and 36″ are available. Note that 12″ of lance length are contained within the unit shroud
- Body Size – 8″ Diameter x 17″ Long x 12″ Base Flange – Suspension Hook 14″ above body
- Customer Requirements – Compressed air source (90-100 PSI), Overhead Hoist, Dry Nitrogen, Argon, or proprietary dry gas
Included with Purchased Unit
- Degas unit, combination air regulator
- filter
- lubricator for air motor
- four rotating lances
Options
- Three leg mounting for support on flat top crucible furnaces
Request QuoteConsulting RequestWatch Video
Return to Hydrogen Porosity Control Equipment page
Related Links
PAS3000 Porosity Analysis System
PAS5000 Porosity Analysis System
Reduced Pressure Tester
Understanding Hydrogen Porosity Control
Informational Links
Case Study – Control of Hydrogen Porosity by Optimizing Analysis of RPT Samples
Fundamentals of Reduced Pressure Test
Penetrant Equipment